Comprimo® - The route to recovery
(C. Ventham, G. Bloemendal)
2023
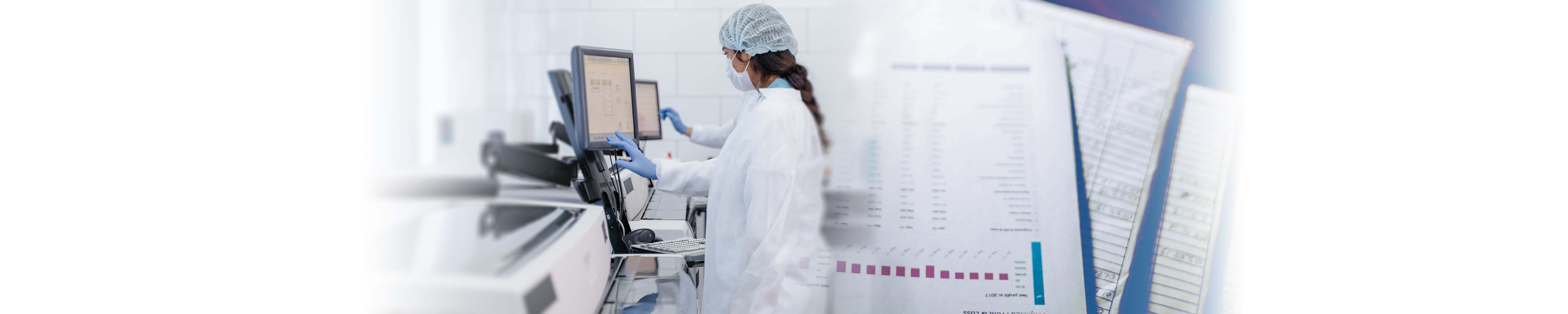
Papers
Comprimo® - SRU Thermal Stage Revamps
(K. Hanlon-Kinsberg, D. Travlos, A. Racz)
2021
Comprimo® - Challenges with the Transition to Biofuels
(M. van Son)
2021
Comprimo® - Sustainability in the Sulphur Recovery Industry
(T. Roelofs, M. van Son)
2019
Troubleshooting Mono Ethylene Glycol Carryover in a Canadian Gas Plant
Laurance Reid Gas Condition Conference
February 26th – March 1st, 2019 – Norman, Oklahoma USA
Comprimo® - Installing Liquid Sulphur Degassing in Existing SRUs
(M. van Son, R. van Grinsven)
2018
Review of Common Design Flaws in Ethylene Glycol Refrigeration Plants and Their Operational Impact
Laurance Reid Gas Condition Conference
February 21th – March1st, 2017 – Norman, Oklahoma USA
Comprimo® - Importance of Heat Maintenance in SRUs
(F. Fatemi, M. van Son)
2016
Comprimo® - The Ten Commandments of Sulphur Recovery
(M. van Son, R. van Grinsven)
2015
Optimizing Ethylene Glycol Refrigeration Process to Maximize NGL Recovery
Laurance Reid Gas Condition Conference
February 22th – 25 th, 2015 – Norman, Oklahoma USA